Manufacturing Process
The Steel billets which are the raw material is heated to 1280°C+ in rotary hearth furnace.

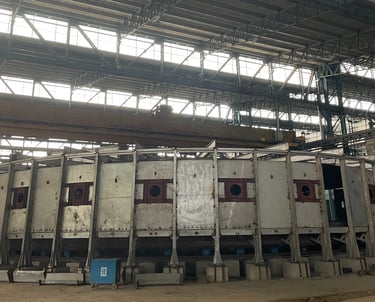
The heated Billets are conveyed to the cross roll piercing mill CRP. The cross roll piercing mill will pierce the steel billets in between two conical rolls driven by two MV Motors and the steel billets will roll over a plug and plug bar to form a hollow.
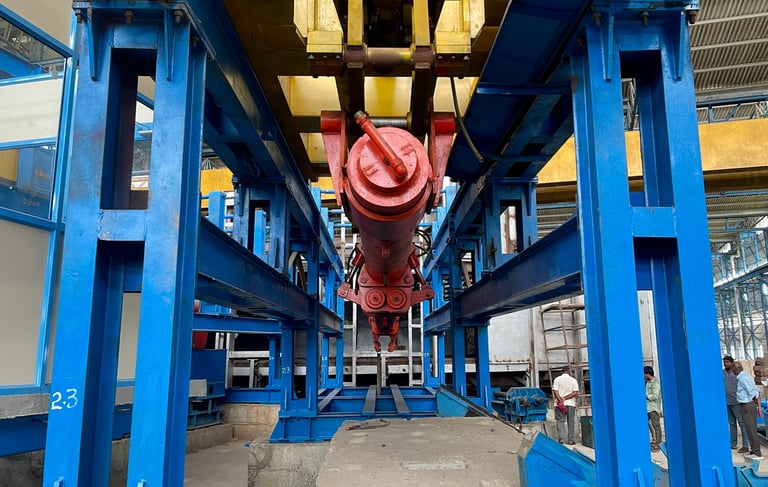
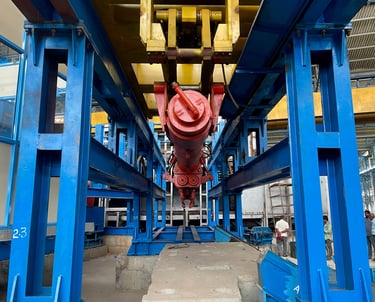
In the second stage, the Hollow is transferred to premium finishing Mill RPF 300 where the Hollow is rolled along with one inserted mandrel bar, to form a pipe with dimensional tolerance. The formed pipe is transferred to extracting mill, where the pipe is separated from mandrel bar. The pipe is transferred to next stage through induction heating system.
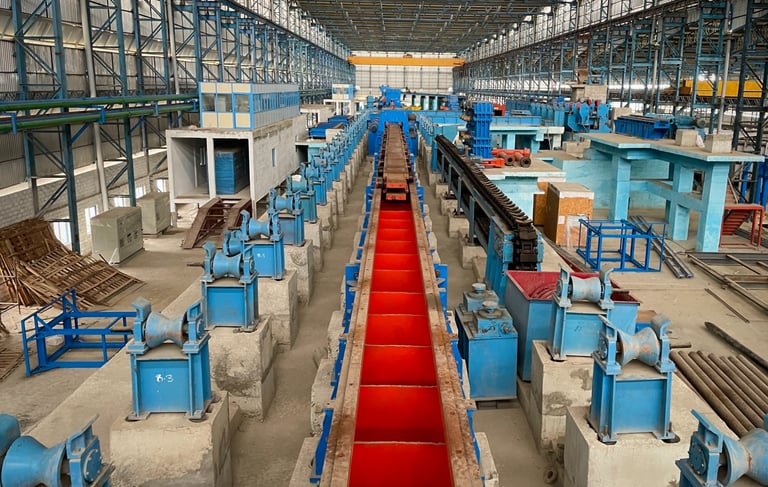
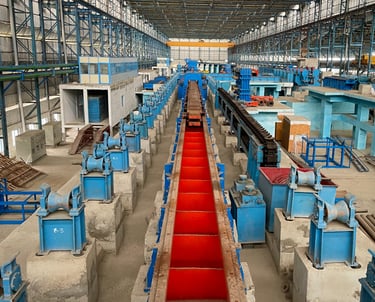
The pipes are rolled in 24 stand stretch reducing mill, where the pipe diameters are reduced to required sizes ranging from 300mm to 38mm
All the mills, cross roll piercing mill, mandrel mill, premium finishing mill, extracting mill and stretch reducing mill are in one production line and each requiring few seconds of operation and by default, the system capacity is at 200,000 Tonnes even after considering maintenance and change over times.
The pipes are further processed in hot finishing section on layers saws, straightening mill, nondestructive testing equipment, edge chamfering and hydro testing machines.
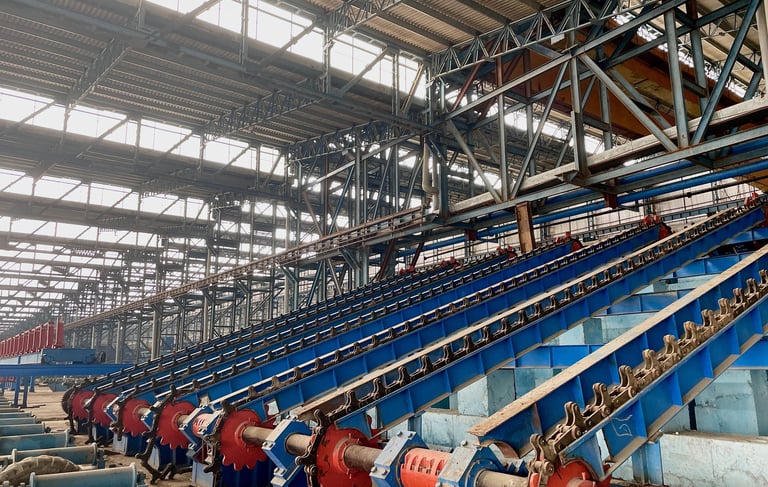
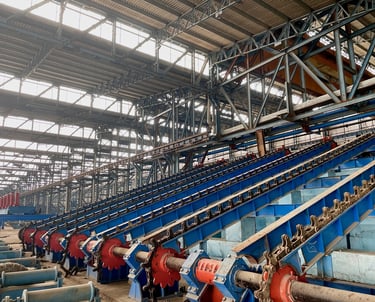
Hot Finishing Mill
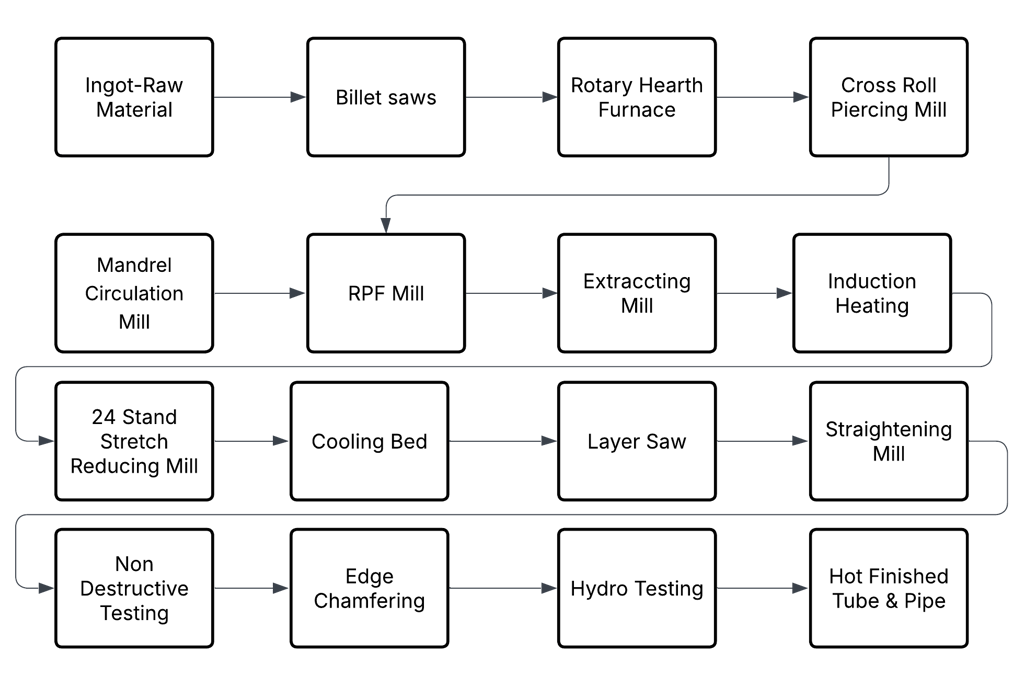
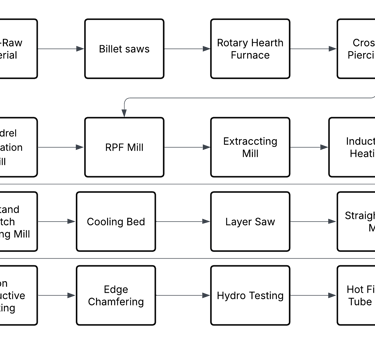
Hot rolled carbon steel seamless pipes & tubes are processed in our cold mill for various applications hydraulic tubes, bearing tubes, hydraulic cylinder & other precision tubes.
Cold drawn seamless pipes & tubes
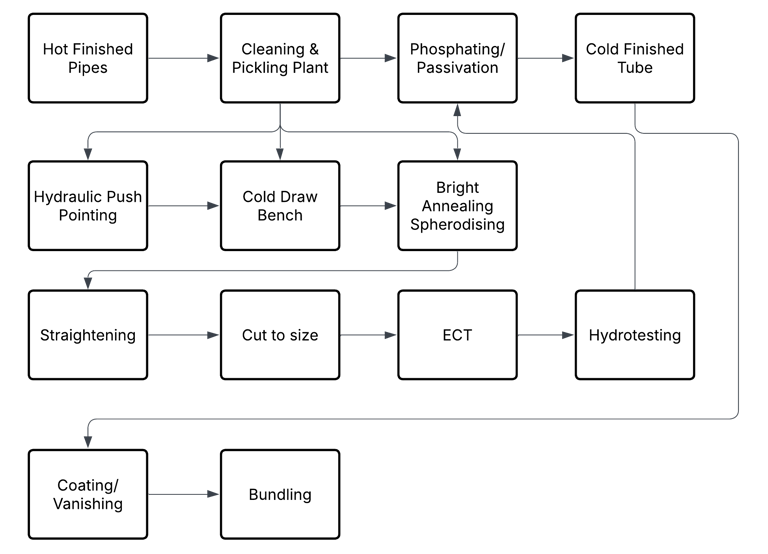
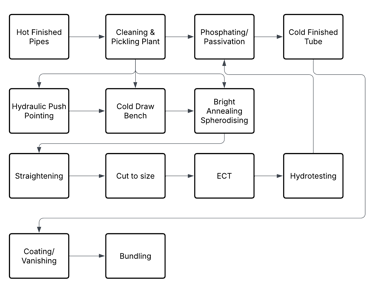
Hot rolled carbon steel seamless pipes & tubes are further processed in our API Mill for production of API grade pipes and tubes.
API Grade seamless pipes & tubes
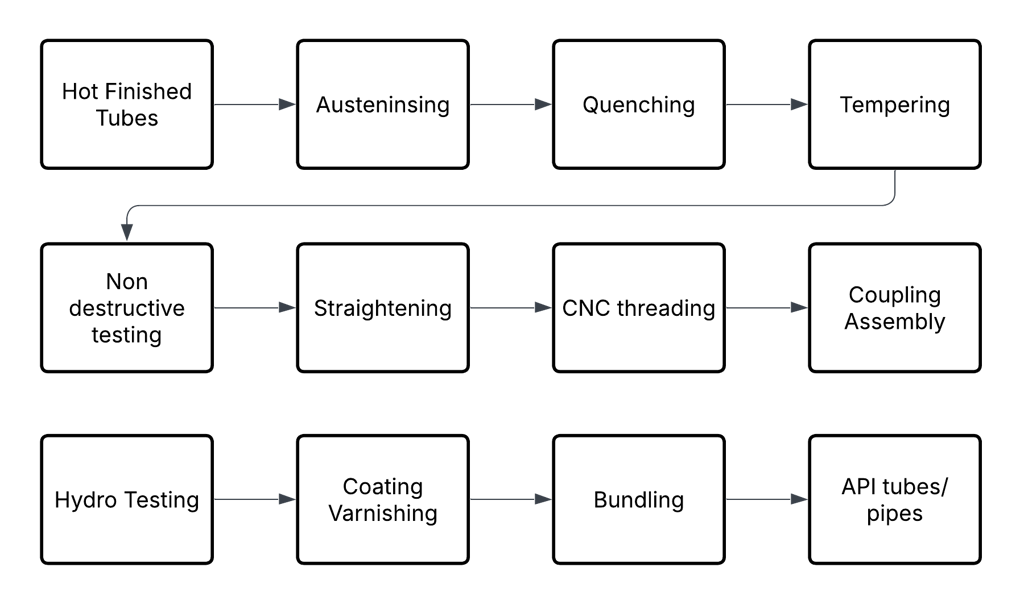
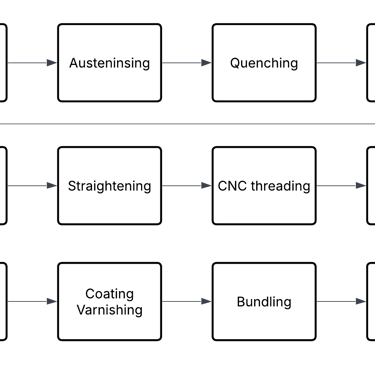
Quality
Precision-engineered seamless pipes for global industries.
redsonengineers@gmail.com
© 2025. All rights reserved.